
Spray drying
Adding value to manufacturing of pharmaceutical formulations with our in-silico strategies.
From the early stage to late stage.
Solvent Selection for Spray Drying
Our in-silico modeling capabilities leverage the PC-SAFT thermodynamic model and advanced kinetic models to optimize solvent selection for spray drying. By accurately predicting solvent behavior, we ensure the identification of the most suitable solvent or solvent mixture. This ensures that all solids are optimally dissolved, creating a homogenous feed solution that is crucial for consistent and efficient spray drying processes.

Solvent Evaporation Prediction
We utilize sophisticated models to predict drying trajectories and solvent accumulation during the spray drying process. Our approach helps identify risks associated with uneven evaporation rates of solvents with different volatilities, which can lead to solvent accumulation and phase separation. By understanding these dynamics, we mitigate risks and ensure a stable and efficient drying process.
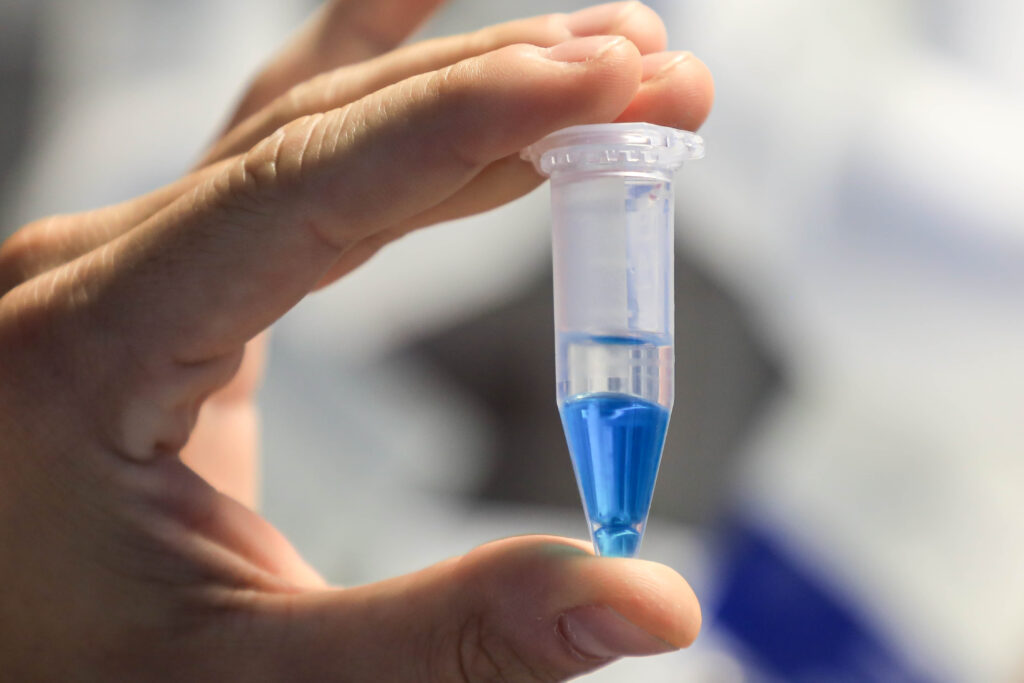
Spray Dryer Process Design and Virtual DOE
Our in-silico tools enable the precise design of spray drying processes. Through virtual Design of Experiments (DOE), we identify the optimal operation points, enhancing efficiency and product quality. This approach allows for rapid experimentation and optimization, reducing the need for extensive physical trials and accelerating development timelines.
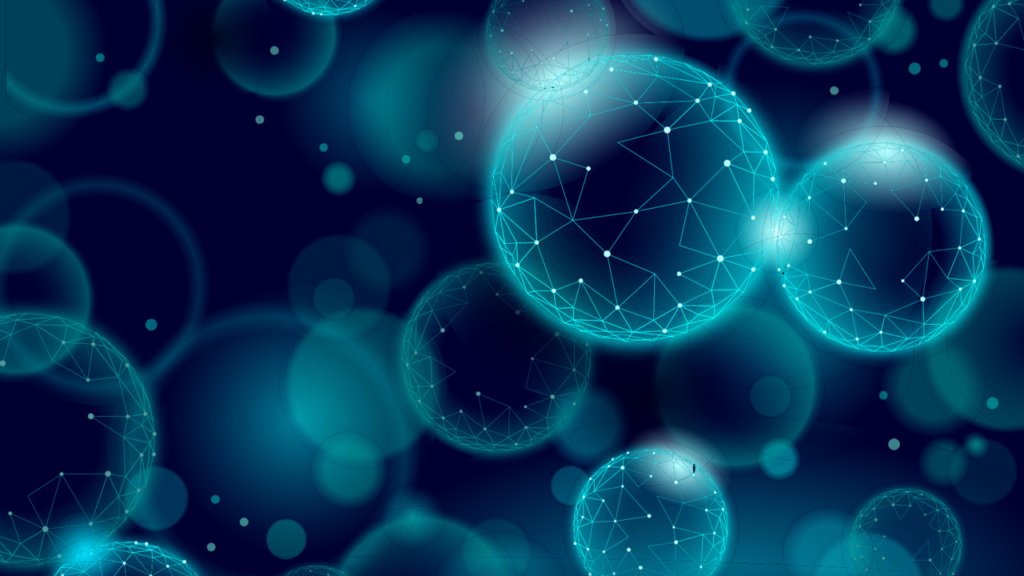
Solvent Content and stability of the Spray-Dried Particles
Using advanced modeling, we assess the solvent content in spray-dried particles and evaluate the stability of intermediates. This includes analyzing the wet glass transition temperature (Tg) and crystallization risk. By ensuring that intermediates remain stable, we improve the overall quality and performance of the final product.
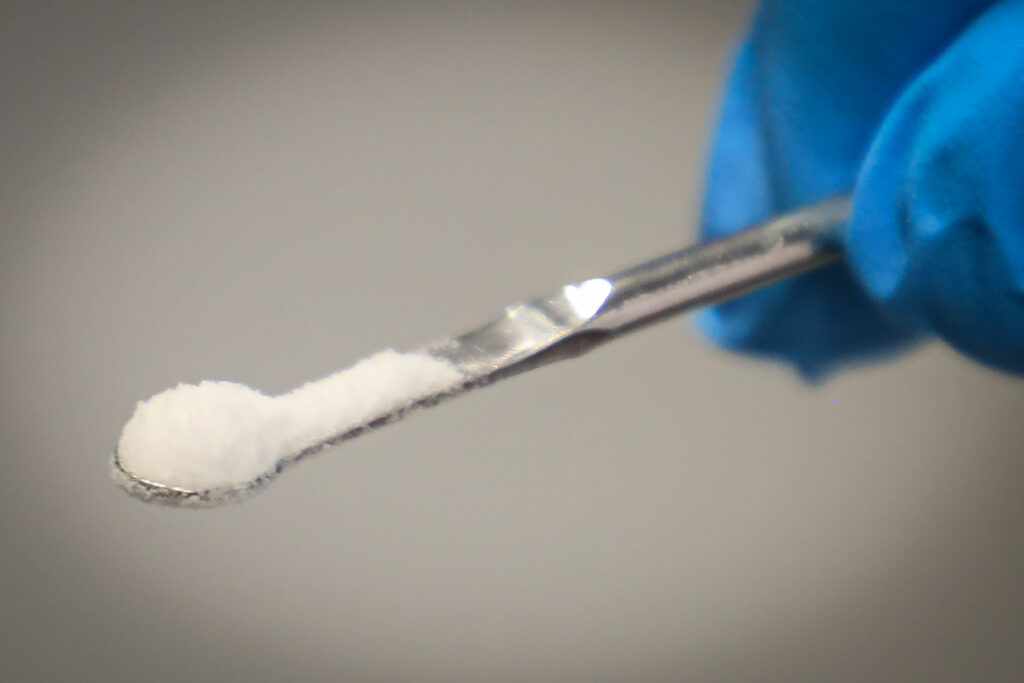
Scale-Up Risk Assessment
We provide comprehensive risk assessments for scaling up from lab-stage to late-stage manufacturing. Our models predict potential challenges and provide solutions to mitigate risks during scale-up. This ensures a smooth transition from small-scale experiments to full-scale production, maintaining product consistency and quality.

Secondary Solvent Drying and Fast Solvent Removal
Our capabilities extend to optimizing secondary drying processes. We focus on reducing secondary drying times and achieving ICH-conform solvent levels safely and efficiently. By modeling solvent removal kinetics, we ensure that the final product meets regulatory requirements while maintaining high quality and stability.
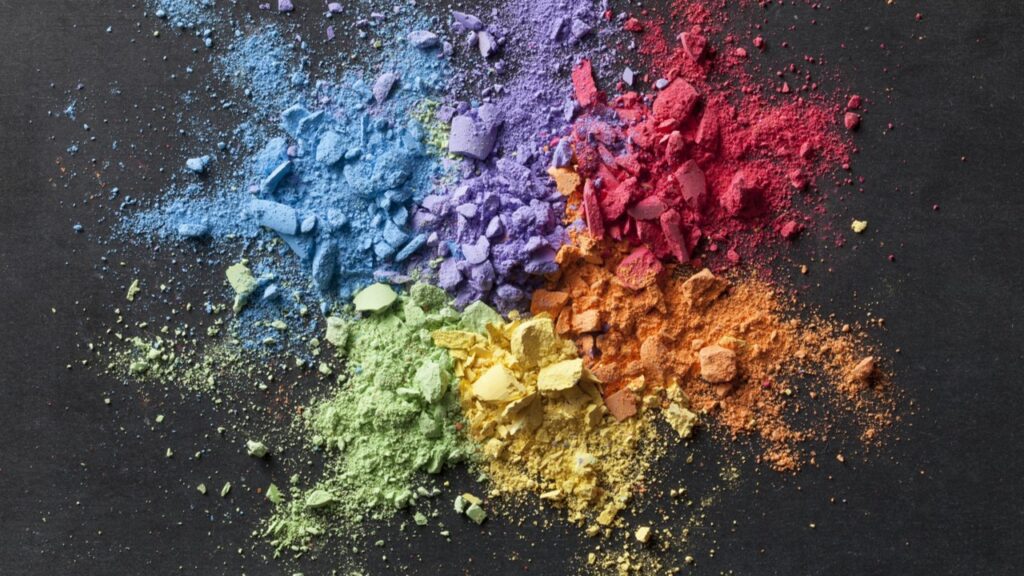
Read more...
Read also our latest blog article about spray drying and our peer-reviewed publications:
Unlock the full potential of your spray drying process.
Get in touch with us today to learn how our advanced in-silico modeling capabilities can solve your spray drying challenges and optimize your production.